Artificial leather ensures quality consistency through careful manufacturing processes and adherence to strict standards and specifications. Here are some key factors that contribute to maintaining quality consistency in artificial leather production:
Controlled Manufacturing Environment: Artificial leather is typically produced in controlled manufacturing environments where factors such as temperature, humidity, and cleanliness are regulated. This helps maintain consistent conditions throughout the production process, reducing the potential for variations in the final product.
Precision in Raw Materials: Manufacturers use precise formulations of raw materials, including polymers, binders, and additives, to achieve the desired properties in the artificial leather. Using consistent and high-quality raw materials is essential for maintaining uniformity in the end product.
Standardized Production Techniques: Adopting standardized production techniques ensures that each batch of artificial leather is manufactured using the same process, minimizing variations between different runs.
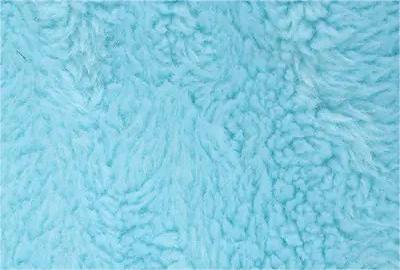
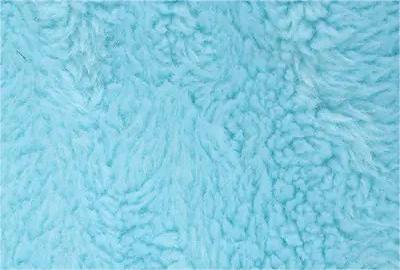
Quality Control and Testing: Rigorous quality control measures are implemented at various stages of production. Regular testing and inspection help identify any deviations from set standards, allowing adjustments to be made to maintain consistency.
Testing Protocols for Performance Properties: Artificial leather undergoes testing to assess its performance properties, such as tensile strength, tear resistance, abrasion resistance, colorfastness, and water repellency. These tests ensure that the product meets established quality and performance standards.
Evaluation of Appearance and Texture: Artificial leather is evaluated for its appearance and texture to ensure that it closely resembles genuine leather or meets specific design requirements.
Feedback and Continuous Improvement: Feedback from customers, industry experts, and internal teams is gathered and analyzed to identify areas for improvement and innovation. Continuous improvement initiatives help enhance product quality over time.
Adherence to Industry Standards: Manufacturers often adhere to international industry standards and certifications, such as ISO (International Organization for Standardization) and ASTM (American Society for Testing and Materials), to ensure that their artificial leather products meet recognized quality benchmarks.
Supplier Qualification: Artificial leather manufacturers carefully select and qualify their raw material suppliers. Establishing strong relationships with reliable suppliers helps ensure consistency in the quality of raw materials used.
Consistent Manufacturing Parameters: Maintaining consistent manufacturing parameters, such as curing temperatures, coating thickness, and drying times, contributes to uniformity in the final product.
By incorporating these practices and quality control measures, artificial leather producers can achieve a high level of quality consistency in their products, providing customers with reliable and uniform materials for various applications, including fashion, upholstery, automotive, and accessories.